Pneumatic Valves & Valve Manifolds on Powermatic Associates
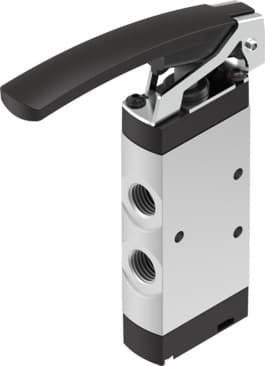
Pneumatic Valves & Valve Manifolds
Valve manifolds and pneumatic valves are essential elements in automated systems, managing the power, speed, and movement direction in pneumatic systems. They control pressure and airflow, guaranteeing efficient functioning in various industries. There are different types of valve manifolds, providing advantages such as streamlined air distribution and saving space. Routine maintenance is crucial for achieving the best performance.
Pneumatic Valves & Valve Manifolds
General Guide & Overview
Pneumatic valves and valve manifolds are crucial components in automated systems, playing a vital role in streamlining operations. These valves are responsible for controlling the force, velocity, and direction of movement of the actuators, ensuring smooth functionality of pneumatic systems.
In pneumatic systems, different types of valves serve specific functions. Pressure relief valves regulate the pressure at the inlet port, preventing excessive pressurization. Pressure regulators, on the other hand, limit pressure downstream and are used in the air preparation stage as well as in the control of cylinders and motors. Flow control valves adjust the velocity of cylinder or motor movement by controlling the airflow. Pneumatic directional valves come in various sizes and configurations and are used to control the airflow direction in the system.
Pneumatic valves and valve manifolds optimize automated systems by providing precise control over the actuators, ensuring efficient operations and improved productivity. With their ability to regulate pressure, control flow, and direct airflow, these components are indispensable in a wide range of industries.
Types of Pneumatic Manifolds
When it comes to pneumatic systems, there are two main types of manifolds to consider: single piece design manifolds and modular block design manifolds. Each option offers its own set of advantages and characteristics that cater to different system requirements and preferences.
Single Piece Design Manifolds:
A single piece design manifold is a preconfigured unit that comes with a specific number of valves and ports. These manifolds are designed to distribute compressed air evenly to all connected components, ensuring smooth and efficient operation. Available in materials such as steel, aluminum, cast iron, or plastic, they are capable of handling high-pressure applications with ease.
Modular Block Design Manifolds:
If customization and flexibility are important factors for your pneumatic system, modular block design manifolds are a great choice. These manifolds consist of individual blocks that can be added or removed to create the desired configuration. By sealing each block with o-rings, these manifolds effectively prevent leakage and can accommodate valves of various sizes.
Pneumatic manifolds are often labeled according to ISO standards, such as ISO 5599 and ISO 15407. These standards define the dimensions, mounting interfaces, and electrical connections of the manifolds, providing a common language for manufacturers and users alike. Recognizable by their manifold symbol, which is a perpendicular intersection of two lines inside a square, they signify multiple connection points and help streamline installation and maintenance processes.
Benefits and Considerations of Pneumatic Manifolds
When it comes to distribution systems, pneumatic manifolds offer a range of benefits that improve the overall efficiency and effectiveness of the system. These benefits include reduced system complexity, cost savings, space-saving, and efficient air distribution.
One of the major advantages of pneumatic manifolds is their ability to simplify the process of air distribution. By connecting multiple outlets to a single source, they eliminate the need for multiple connections and significantly reduce the risk of leakage. This not only streamlines the system but also improves its reliability and safety.
Additionally, pneumatic manifolds allow for better utilization of resources and can create a more organized and compact distribution system. With their interchangeable blocks and plates, they offer adaptability and flexibility. This means that additional components can be easily added or removed as needed, making them highly versatile and responsive to changing system requirements.
When selecting a pneumatic manifold, several criteria should be taken into consideration. The number of valve stations and ports is a crucial factor in determining the manifold's capacity. The choice of material, whether stainless steel, aluminum, or plastic, should align with the system's specific needs and requirements. Furthermore, the mounting pattern should match the system's layout to ensure proper installation and operation.
Regular maintenance and troubleshooting are essential for the proper functioning and durability of pneumatic manifolds. By adhering to a maintenance schedule, potential issues can be detected and addressed early, ensuring the system operates at its optimal level.
In conclusion, pneumatic manifolds provide numerous benefits in distribution systems, such as reduced complexity, cost savings, space-saving, and efficient air distribution. Their adaptability and ease of maintenance make them a valuable asset for various industries. With proper selection, installation, and routine maintenance, pneumatic manifolds can enhance the performance and reliability of pneumatic systems, leading to improved overall productivity and efficiency.
Pneumatic valves and valve manifolds are of utmost importance in optimizing pneumatic systems and achieving efficient automation, resulting in improved productivity. These components provide safe and precise control over actuators, allowing for the regulation of force, velocity, and direction of movement. By utilizing pneumatic valves and valve manifolds, companies can streamline their operations, streamline their operations, and achieve cost savings.
Pneumatic manifolds play a crucial role in enhancing the efficiency of distribution systems by simplifying the process of air distribution, reducing complexity, and saving valuable space. They enable multiple outlets to be connected to a single source, eliminating the need for numerous connections and reducing the risk of leakage. Moreover, selecting the appropriate pneumatic manifold and performing routine maintenance are essential to ensure reliable operation and prevent system failures.
In summary, pneumatic valves and valve manifolds are essential components in a wide range of industries, improving automation and productivity. By optimizing pneumatic systems and utilizing these components, companies can achieve efficient operations, cost savings, and streamlined processes. With their numerous benefits and functionalities, pneumatic valves and valve manifolds contribute significantly to the success and innovation of modern industries.
FAQ
Pneumatic valves control the force, velocity, and direction of movement of actuators in compressed air pneumatic systems. They regulate pressure, control flow, and direct airflow within the system to ensure efficient and safe operation.
There are two main types of pneumatic manifolds: single piece design manifolds and modular block design manifolds. Single piece design manifolds come preconfigured with a specific number of valves and ports, while modular block design manifolds allow for customization by adding or removing individual blocks.
The manifold symbol is a perpendicular intersection of two lines inside a square, representing multiple connection points. It helps identify pneumatic manifolds that conform to ISO standards and indicates the presence of a distribution point in the system.
Pneumatic manifolds simplify air distribution by connecting multiple outlets to a single source, reducing system complexity and the risk of leakage. They also save space, allow for efficient resource utilization, and create a more organized distribution system.
When selecting a pneumatic manifold, factors such as the number of valve stations, the number of valve ports, material (stainless steel, aluminum, or plastic), and the mounting pattern must be considered to ensure compatibility with the system requirements.
Routine maintenance is essential to ensure proper functioning and durability of pneumatic manifolds. Regular inspections, cleaning, and troubleshooting can help identify and address any issues, preventing system failures and maximizing performance.
Pneumatic valves and valve manifolds provide precise control over actuators, enabling efficient automation and improved productivity. By simplifying air distribution and reducing complexity, they streamline operations, optimize pneumatic systems, and result in cost savings.
Pneumatic valves and valve manifolds play a crucial role in a wide range of industries by ensuring safe and precise control over automation processes. Their ability to control force, velocity, and movement direction contributes to efficient operation and increased productivity.