Festo Pneumatic Accessories on Powermatic Associates
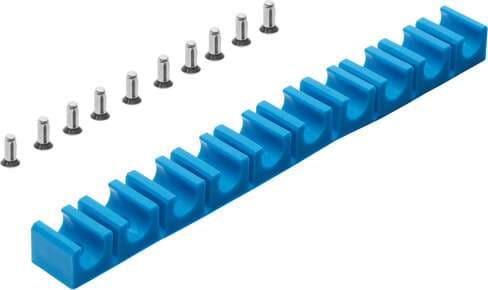
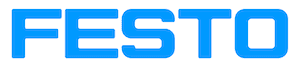
Pneumatic Accessories- Festo
Accessories for pneumatic systems, such as air hoses, tubes, valves, and cylinders, are crucial elements that facilitate uninterrupted airflow and connections between the pneumatic components.
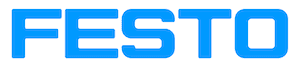