Robotic Parts on Powermatic Associates
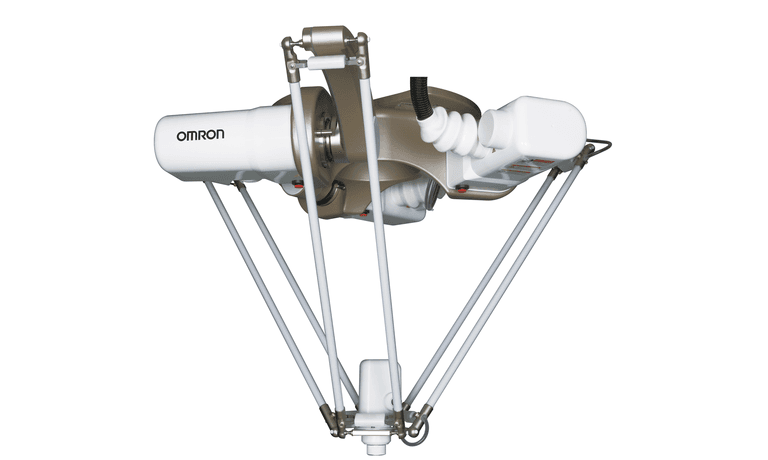
Robotic Parts
Essential elements in automation, robotic parts such as the robotic arm, end-effector, motors, controller, and sensors, enable robots to carry out tasks effectively. Gaining knowledge about these components aids in constructing dependable robotic systems that enhance productivity.
Subcategories (2)
Found 9,518 products
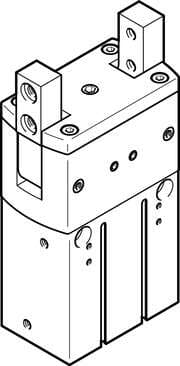
radial gripper HGRT-32-A-G2 With gripping force backup when closing...-G2. Size: 32, Max. replacement accuracy: <: 0,2 mm, Max. angular gripper jaw backlash ax,ay: <: 0,1 deg, Max. opening angle: 180 deg, Rotationally symmetrical: <: 0,2 mm
Quick Quote
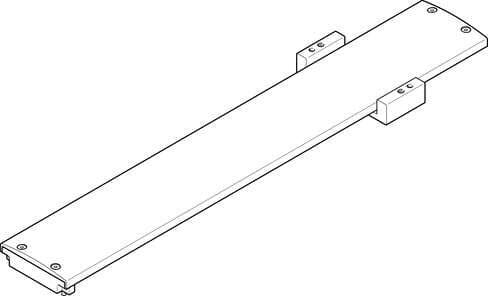
cover kit EASC-S1-46-640-S For covering the axis profile which is open at the top. Size: 46, Assembly position: Any, Corrosion resistance classification CRC: 2 - Moderate corrosion stress, Ambient temperature: -10 - 60 °C, Product weight: 1190 g
Quick Quote
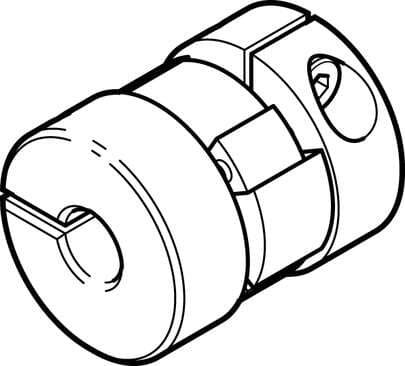
coupling EAMC-16-20-4-6 Holder diameter 1: 4 mm, Holder diameter 2: 6 mm, Size: 16, Nominal length: 20 mm, Assembly position: Any
Quick Quote
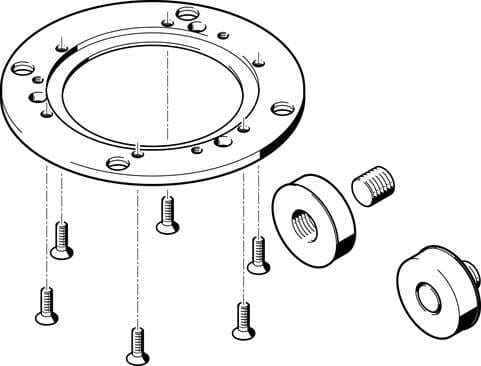
indexing conversion kit DADM-CK-140-6 For rotary indexing table DHTG. Size: 140, Corrosion resistance classification CRC: (* 2 - Moderate corrosion stress, * (when installed)), Materials note: (* Free of copper and PTFE, * Conforms to RoHS), Material plat
Quick Quote
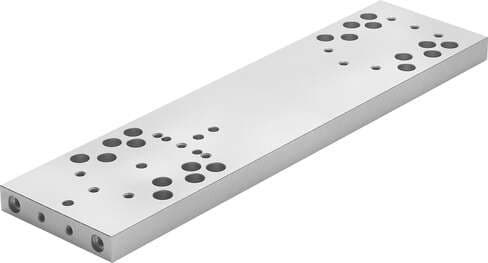
basic kit HMVD-RP/FP-DL25/40 For multi-axis modular systems from the handling and assembly technology range. Assembly position: Any, Corrosion resistance classification CRC: 2 - Moderate corrosion stress, Product weight: 1000 g, Materials note: Free of co
Quick Quote
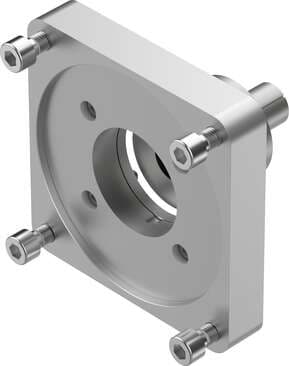
axial kit EAMM-A-K62-140A Suitable for electric drives. Assembly position: Any, Storage temperature: -25 - 60 °C, Relative air humidity: 0 - 95 %, Protection class: IP40, Ambient temperature: -10 - 60 °C
Quick Quote
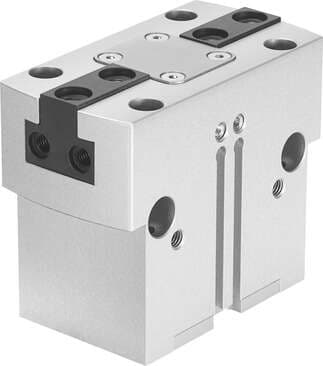
parallel gripper HGPT-40-A-B-G1 sturdy, with gripping force retention when opening ...-G1. Size: 40, Stroke per gripper jaw: 10 mm, Max. replacement accuracy: <: 0,2 mm, Max. angular gripper jaw backlash ax,ay: <: 0,1 deg, Max. gripper jaw backlash Sz:
Quick Quote
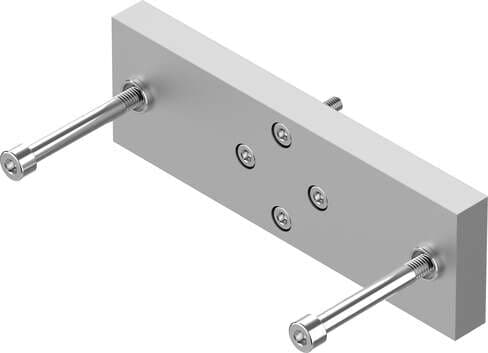
adapter kit DHAA-D-E21-70...110-Q11-50 Assembly position: Any, Corrosion resistance classification CRC: 2 - Moderate corrosion stress, Product weight: 627 g, Mounting type: (* With through-hole and screw, * with centring sleeve), Materials note: Conforms
Quick Quote
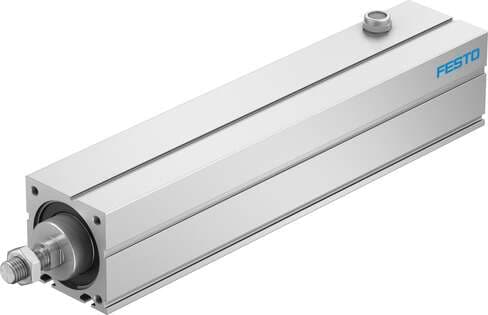
electric cylinder EPCC-BS-60-175-5P-A Size: 60, Stroke: 175 mm, Stroke reserve: 0 mm, Piston rod thread: M12x1,25, Reversing backlash: 100 µm
Quick Quote
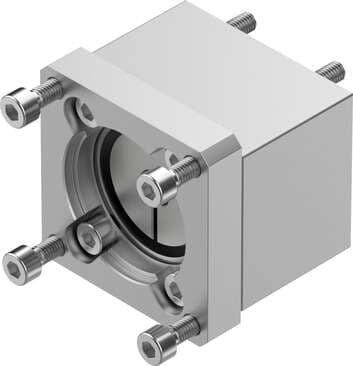
axial kit EAMM-A-S38-55A-G2 Suitable for electric drives. Assembly position: Any, Storage temperature: -25 - 60 °C, Relative air humidity: 0 - 95 %, Protection class: IP40, Ambient temperature: -10 - 60 °C
Quick Quote
Item | Manufacturer | Price | Stock | Delivery | |
---|---|---|---|---|---|
![]() | 563911 radial gripper HGRT-32-A-G2 With gripping force backup when closing...-G2. Size: 32, Max. replacement accuracy: <: 0,2 mm, Max. angular gripper jaw backlash ax,ay: <: 0,1 deg, Max. opening angle: 180 deg, Rotationally symmetrical: <: 0,2 mm | Festo | Quick Quote | ||
![]() | 562740 cover kit EASC-S1-46-640-S For covering the axis profile which is open at the top. Size: 46, Assembly position: Any, Corrosion resistance classification CRC: 2 - Moderate corrosion stress, Ambient temperature: -10 - 60 °C, Product weight: 1190 g | Festo | Quick Quote | ||
![]() | 562673 coupling EAMC-16-20-4-6 Holder diameter 1: 4 mm, Holder diameter 2: 6 mm, Size: 16, Nominal length: 20 mm, Assembly position: Any | Festo | Quick Quote | ||
![]() | 548111 indexing conversion kit DADM-CK-140-6 For rotary indexing table DHTG. Size: 140, Corrosion resistance classification CRC: (* 2 - Moderate corrosion stress, * (when installed)), Materials note: (* Free of copper and PTFE, * Conforms to RoHS), Material plat | Festo | Quick Quote | ||
![]() | 539655 basic kit HMVD-RP/FP-DL25/40 For multi-axis modular systems from the handling and assembly technology range. Assembly position: Any, Corrosion resistance classification CRC: 2 - Moderate corrosion stress, Product weight: 1000 g, Materials note: Free of co | Festo | Quick Quote | ||
![]() | 557993 axial kit EAMM-A-K62-140A Suitable for electric drives. Assembly position: Any, Storage temperature: -25 - 60 °C, Relative air humidity: 0 - 95 %, Protection class: IP40, Ambient temperature: -10 - 60 °C | Festo | Quick Quote | ||
![]() | 560217 parallel gripper HGPT-40-A-B-G1 sturdy, with gripping force retention when opening ...-G1. Size: 40, Stroke per gripper jaw: 10 mm, Max. replacement accuracy: <: 0,2 mm, Max. angular gripper jaw backlash ax,ay: <: 0,1 deg, Max. gripper jaw backlash Sz: | Festo | Quick Quote | ||
![]() | 5154639 adapter kit DHAA-D-E21-70...110-Q11-50 Assembly position: Any, Corrosion resistance classification CRC: 2 - Moderate corrosion stress, Product weight: 627 g, Mounting type: (* With through-hole and screw, * with centring sleeve), Materials note: Conforms | Festo | Quick Quote | ||
![]() | 5428894 electric cylinder EPCC-BS-60-175-5P-A Size: 60, Stroke: 175 mm, Stroke reserve: 0 mm, Piston rod thread: M12x1,25, Reversing backlash: 100 µm | Festo | Quick Quote | ||
![]() | 3637967 axial kit EAMM-A-S38-55A-G2 Suitable for electric drives. Assembly position: Any, Storage temperature: -25 - 60 °C, Relative air humidity: 0 - 95 %, Protection class: IP40, Ambient temperature: -10 - 60 °C | Festo | Quick Quote |
Robotic Parts
General Guide & Overview
In the world of industrial automation and robotics, robotic systems play a crucial role in enhancing productivity and efficiency. Behind the remarkable capabilities of these robots lie the intricate integration of various robotic parts.
Building industrial robots requires a deep understanding of the components that make them function seamlessly. From the robotic arm to the sensors, each part serves a specific purpose, contributing to the overall performance of the robot.
Modern advancements in technology have revolutionized the design and functionality of robotic parts, making them faster, more compact, and affordable. These advancements have significantly impacted industries such as automotive, heavy machinery, and railways, where industrial robots have become indispensable.
Industrial robots are typically comprised of five main components: the robotic arm, end-effector, motors, controller, and sensors. While the specific parts may vary based on the robot design, these core components form the foundation of most industrial robots.
By understanding the intricacies of these robotic parts and their integration into a robot system, companies can build and maintain reliable and efficient robotic systems. This knowledge is vital for selecting reputable industrial robot manufacturers who prioritize the quality and workmanship of their robotic parts.
The Parts of an Industrial Robot
The robotic arm, also known as the manipulator, is the part of the robot that performs various tasks. It is made up of a shoulder, elbow, and wrist, similar to a human arm. The end-effector, also called the robot's hand, is a tool device attached to the wrist of the robotic arm. It provides the robot with more dexterity and enables it to perform specific tasks.
Motors play a crucial role in powering the robotic parts and facilitating their movement. They provide the necessary torque and control for the robotic arm to perform precise actions. The controller, often referred to as the brain of the robot, is responsible for controlling all the other parts and executing commands based on the desired task.
The Role of Sensors
Sensors are essential components of an industrial robot as they detect and measure parameters in the robot's environment, ensuring safety and control. These sensors can include proximity sensors, force sensors, vision sensors, and more. They provide crucial feedback to the controller, allowing the robot to adapt and respond to its surroundings.
The integration of these different parts creates a powerful and versatile industrial robot. The structure of the robot is designed for optimal performance and efficiency, allowing it to carry out complex tasks with precision. From the robust robotic arm to the highly sensitive sensors, each component plays a vital role in the overall functionality of the robot.
Robot Motion and Control Systems
Robots can have different types of control systems that determine their behavior. Control systems play a crucial role in enabling robots to perform tasks accurately and efficiently.
Pre-Programmed Robots
Pre-programmed robots follow a fixed program that dictates their actions. These robots are ideal for performing repetitive tasks with minimal environmental input. By executing a sequence of predefined commands, pre-programmed robots can complete specific tasks on a loop, ensuring consistency and precision.
Autonomous Robots
Autonomous robots are designed to adapt to changes in their environment. These robots utilize sensors to gather information about their surroundings, enabling them to make decisions and perform tasks based on real-time data. Autonomous robots are capable of navigating complex environments, adjusting their actions accordingly to achieve their objectives efficiently.
Sensors: Gathering Environmental Information
Sensors are essential components of robot control systems. They detect and measure various aspects of the environment, providing robots with valuable information to make informed decisions. Robots employ a wide range of sensors, including visual sensors for capturing images, sound sensors for detecting auditory signals, collision sensors for avoiding obstacles, temperature sensors for measuring heat levels, and pressure sensors for determining the force in a given area.
Effectors: Enabling Robot Work
Effectors are the parts of the robot that perform the actual work. They include end-effectors or tools attached to the robotic arm. These effectors enable robots to interact with their surroundings, manipulate objects, and carry out specific tasks. Examples of effectors include grippers, welding tools, or even specialized equipment designed for specific applications.
Understanding the different parts of an industrial robot is crucial for the successful construction and maintenance of robotic systems. The quality and integration of these robotic parts play a significant role in determining the overall performance and reliability of the system. Therefore, it is essential for businesses to select reputable industrial robot brands that prioritize the excellence and craftsmanship of their components.
By choosing a reliable manufacturer, companies can ensure that they are utilizing high-quality robotic parts that meet industry standards. These parts, when integrated into the robotic structure, contribute to enhancing the overall robot performance, leading to increased productivity, improved product quality, and operational efficiency.
Moreover, having a basic understanding of robot structures and the functions of different parts also helps in the effective implementation of robots across various industries. With this knowledge, businesses can identify the specific robotic parts required for their applications and harness their capabilities accordingly. This understanding enables companies to optimize the robot's performance and tailor it to their unique requirements, thereby maximizing their return on investment.
FAQ
What are some of the main parts of an industrial robot?
The main parts of an industrial robot include the robotic arm, end-effector, motors, controller, and sensors.
What is the robotic arm and what does it do?
The robotic arm, also known as the manipulator, performs various tasks and is made up of a shoulder, elbow, and wrist, similar to a human arm.
What is the end-effector and why is it important?
The end-effector is a tool device attached to the wrist of the robotic arm, providing the robot with more dexterity and enabling it to perform specific tasks.
What role do motors play in industrial robots?
Motors are used to power the robotic parts and facilitate their movement.
What is the controller in an industrial robot?
The controller serves as the brain of the robot, controlling all other parts and executing commands.
Why are sensors important in industrial robots?
Sensors detect and measure various parameters in the robot's environment, ensuring safety and control.
How do pre-programmed robots differ from autonomous robots?
Pre-programmed robots perform repetitive actions based on a fixed program and limited environmental input, while autonomous robots can adapt to changes in complex environments.
What do sensors do in industrial robots?
Sensors gather information about the surroundings, such as visual information, sound, collision detection, temperature, and pressure.
What are effectors in an industrial robot?
Effectors are the parts of the robot that actually perform the work, such as end-effectors or tools attached to the robotic arm.
How important is understanding the different parts of an industrial robot?
Understanding the different parts of an industrial robot is essential for building and maintaining robotic systems, improving performance, reliability, and efficiency.