All categories
Compressed Air Preparation Accessories
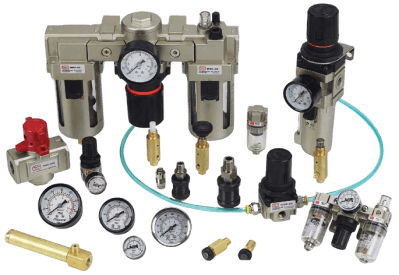
Compressed Air Preparation Accessories
Accessories for preparing compressed air are comprised of systems and components that enhance the reliability of processes, the availability of machines, and the lifespan of compressed air systems. These accessories guarantee that the compressed air is devoid of particles, water, and oils, and maintains the appropriate level of purity, flow rate, and operating pressure.
Compressed Air Preparation Accessories
General Guide & Overview
Compressed air is a vital resource in modern production companies, providing speed, power, precision, and safe handling. However, the presence of particles, water, and oils in compressed air can compromise the service life and functionality of components and systems, leading to reduced productivity and energy efficiency.
Proper preparation of compressed air is essential to improve process reliability, machine availability, and the overall service life of components. This requires ensuring a suitable level of compressed air purity, a sufficient amount of compressed air, and the correct operating pressure.
Compressed air preparation accessories play a crucial role in achieving these goals. They include various components and elements that enhance the performance and reliability of the compressed air system. By investing in the right accessories, companies can ensure a clean and dry air supply, proper air distribution, and longer equipment life.
Understanding Air Compressors and Their Operation
An air compressor is a mechanical device that plays a vital role in various industries. Its primary function is to increase the pressure of atmospheric air by reducing its volume. The process involves drawing in ambient air through an intake valve and compressing it using different methods, such as pistons, rotating screws, or vanes.
Once the air is compressed, it undergoes cooling before being stored in a tank for on-demand use. This cooling process is essential to remove excess heat generated during compression, ensuring the compressed air remains at an optimal temperature for further applications.
Air compressors have a wide range of applications and are commonly used for powering pneumatic tools, operating machinery, and controlling industrial processes. They are also instrumental in tasks such as air blasting, spray painting, and material handling.
There are several types of air compressors available in the market, each designed to suit specific needs and applications:
1. Rotary Screw Compressors
Rotary screw compressors are widely used in industrial settings due to their durability and high efficiency. They operate by trapping air between rotating screws, which compresses the air as it moves towards the discharge port.
2. Rotary Vane Compressors
Rotary vane compressors utilize a series of vanes that rotate inside a chamber to compress the air. They are known for their compact design and quiet operation, making them suitable for small-scale applications.
3. Reciprocating Compressors
Reciprocating compressors feature a piston and cylinder arrangement, where the piston moves back and forth to compress the air. These compressors are versatile and commonly used in applications that require high pressures.
4. Oil-Injected Air Compressors
Oil-injected air compressors use oil for lubrication and cooling, ensuring smooth operation and extended lifespan of the compressor. These compressors are ideal for demanding applications that require continuous operation.
5. Oil-Free Air Compressors
Oil-free air compressors, as the name suggests, operate without the need for oil lubrication. They are preferred in applications where air purity is critical, such as in the pharmaceutical and food industries.
6. Fixed Speed Compressors and Variable Speed Drive Compressors
Fixed speed compressors operate at a constant speed, which is suitable for applications with a consistent and predictable air demand. On the other hand, variable speed drive compressors adjust their speed according to the air demand, resulting in energy savings and greater efficiency.
Understanding the different types of air compressors and their operation is crucial for selecting the right compressor for specific applications and optimizing performance. Whether it's powering industrial tools, supporting machinery operations, or controlling industrial processes, the right air compressor can greatly enhance productivity and efficiency in various industries.
The Importance of Air Dryers and Compressed Air System Elements
In a compressed air system, air dryers are essential components that play a critical role in ensuring a clean and dry air supply. One of the main challenges in compressed air systems is the presence of excess water or moisture, which can severely impact the performance and longevity of the system. Air dryers effectively remove this excess water, allowing for proper air treatment and distribution.
There are different types of air dryers available to suit specific requirements. One commonly used type is refrigerated dryers, which cool the compressed air to remove moisture. These dryers are effective for most applications, providing clean and dry air for the system. However, for applications that require an even lower dew point or in environments with extremely low temperatures, desiccant dryers are used. Desiccant dryers use a drying agent, such as silica gel or activated alumina, to absorb moisture, ensuring the air is exceptionally dry.
In addition to air dryers, a well-designed compressed air system should include other important elements such as air receivers, piping networks, pressure regulators, filters, lubricators, control valves, and gauges. These components work together to maintain the proper air pressure, filter out contaminants, regulate the flow of air, and ensure the system operates efficiently. By incorporating these elements, the system can achieve optimal air treatment, distribution, and energy savings.
Having clean and dry air is crucial for many industries as it can significantly impact the performance, reliability, and lifespan of equipment. Excess moisture can corrode machinery, damage tools, and compromise the quality of the end product. By investing in air dryers and implementing proper system design, companies can enjoy longer equipment life, improved productivity, and energy savings.
FAQ
What are compressed air preparation accessories?
Compressed air preparation accessories include components and systems designed to improve process reliability, machine availability, and the service life of compressed air systems. These accessories ensure the compressed air is clean, free from particles, water, and oils, and has the suitable level of compressed air purity, flow rate, and operating pressure.
How does an air compressor work?
An air compressor is a mechanical device that increases the pressure of atmospheric air by reducing its volume. It draws in ambient air through an intake valve and uses methods such as pistons, rotating screws, or vanes to compress it. The compressed air is then cooled, stored in a tank, and delivered for various applications, such as powering pneumatic tools, operating machinery, or controlling industrial processes.
What types of air dryers are available?
There are different types of air dryers available for removing excess water from compressed air. Refrigerated dryers use a cooling process to condense and separate the moisture, while desiccant dryers use adsorption to remove water vapor. The choice of air dryer depends on the specific application and dew point requirements.
Why are air dryers important in a compressed air system?
Air dryers play a critical role in removing excess water from the compressed air to ensure a clean and dry air supply. They are essential for proper air treatment and distribution in a compressed air system. By removing moisture, air dryers help prolong equipment life, prevent corrosion, and enhance energy efficiency, resulting in cost savings and improved productivity.
What other elements are important in a compressed air system?
In addition to air dryers, other important elements in a compressed air system include air receivers, piping network, pressure regulators, filters, lubricators, control valves, and gauges. These components help regulate and control the flow, pressure, and quality of compressed air, ensuring efficient operation and reliable performance of downstream equipment and processes.